Japan, a nation renowned for its meticulous craftsmanship and technological prowess, has established itself as a global leader in the production of anaerobic glove boxes. These precision-engineered chambers, designed to exclude oxygen and moisture, are indispensable tools in fields ranging from materials science to electronics. This article delves into the intricacies of their design, manufacture, and application, highlighting the unique contributions of Japanese manufacturers.
The Anaerobic Environment
An anaerobic environment is characterized by the absence of oxygen. This condition is critical for numerous scientific and industrial processes. Materials that readily oxidize, such as alkali metals, pyrophoric compounds, and certain organic compounds, require isolation from atmospheric oxygen to prevent degradation or ignition. The anaerobic glove box provides this controlled atmosphere.
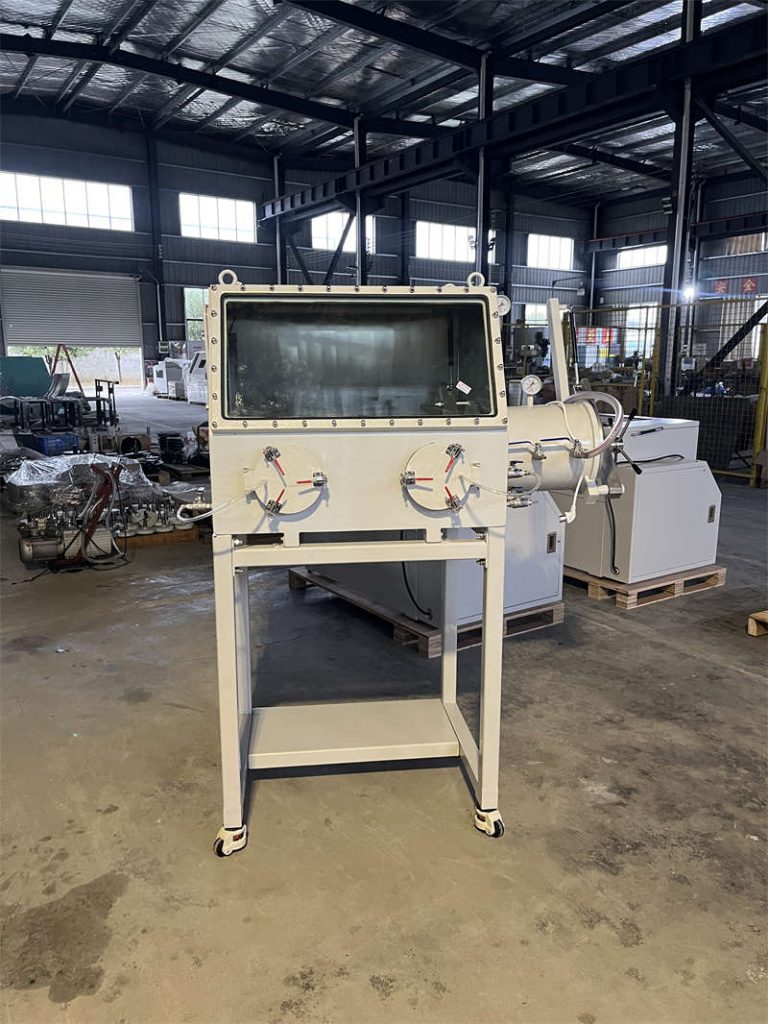
The design of an anaerobic glove box is a complex interplay of materials science, fluid dynamics, and engineering. The primary components are the chamber, the glove ports, the purification system, and the atmosphere control system.
Materials: The Foundation of Integrity
The choice of materials for an anaerobic glove box is paramount. Stainless steel, often 316L for its corrosion resistance, is the predominant material for the chamber. Its smooth surface finish minimizes particle retention and facilitates cleaning.
Glove materials must be impermeable to oxygen and water vapor while offering sufficient dexterity. Nitrile and butyl rubber are common choices, but specialized materials may be required for specific applications.
Seals, crucial for maintaining the anaerobic environment, are typically made of fluoropolymers like Viton or Kalrez. These materials exhibit excellent chemical resistance and low permeability to gases.
Design Considerations: A Symphony of Engineering
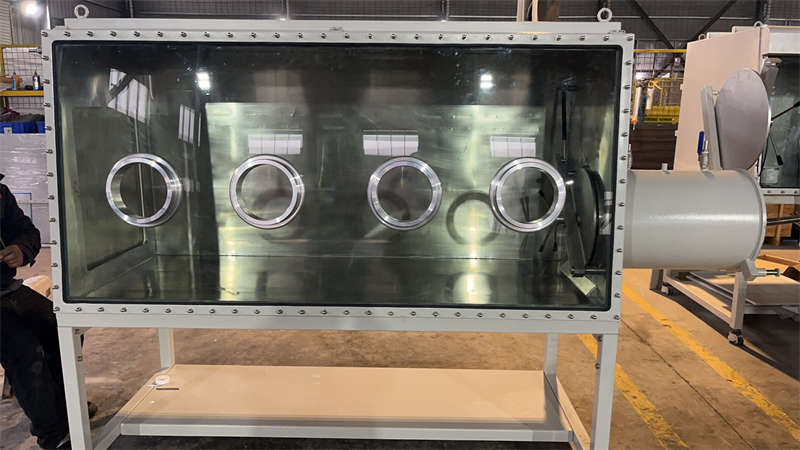
The design of an anaerobic glove box is focused on achieving and maintaining an oxygen-free atmosphere. This requires meticulous attention to detail.
Source icon
Chamber Geometry: The chamber must be designed to minimize dead spaces where oxygen could accumulate. Smooth, rounded corners and a streamlined interior are essential.
Purification System: This system is the heart of the glove box. It typically employs a combination of copper catalysts, molecular sieves, and oxygen sensors to remove oxygen and moisture. The design must ensure efficient and continuous purification.
Atmosphere Control: Precise control of the internal atmosphere is achieved through a combination of vacuum pumps, gas inlets, and pressure regulators. The system must maintain a stable negative pressure relative to the ambient environment to prevent air ingress.
Glove Ports: The design of glove ports must balance the need for operator comfort with the requirement for a secure seal. The glove material and the port interface must be compatible to prevent leaks.
Manufacturing Mastery: Japanese Precision
Japanese manufacturers have elevated glove box production to an art form. Their commitment to quality and attention to detail is evident in every aspect of the manufacturing process.
Cleanroom Environment: Many glove box manufacturers operate in cleanroom facilities to minimize contamination. This ensures that the glove boxes themselves are free from contaminants before being introduced into the critical environment.
Welding Expertise: Welding is a critical process in glove box construction. Japanese manufacturers excel in TIG and laser welding, producing strong and hermetic seals.
Quality Control: Rigorous quality control measures are in place. Leak testing, pressure cycling, and oxygen level monitoring are essential steps in the manufacturing process.
Applications: Expanding Horizons
Anaerobic glove boxes find applications in a wide range of industries. In materials science, they are used for the synthesis of air-sensitive compounds. In the chemical industry, they are employed for handling pyrophoric reagents. In the electronics industry, they provide a controlled environment for the fabrication of sensitive components.
Japanese manufacturers have been at the forefront of developing specialized glove boxes for niche applications. For example, glove boxes designed for lithium-ion battery research incorporate features such as inert gas circulation and temperature control.
The Future of Anaerobic Glove Boxes
The future of anaerobic glove box technology is marked by innovation and sustainability. Advances in materials science, sensor technology, and automation are driving the development of new and improved glove box designs.
There is a growing emphasis on reducing the environmental impact of glove box manufacturing. This includes the use of recycled materials, energy-efficient components, and waste reduction strategies.
In conclusion, Japanese anaerobic glove box manufacturers have established a global reputation for excellence. Their dedication to precision engineering and quality craftsmanship has resulted in products that are essential tools for researchers and engineers around the world. As the demand for controlled environments continues to grow, these manufacturers are well-positioned to meet the evolving needs of their customers.
Note: This article provides a foundational overview of Japanese anaerobic glove box manufacturers. To delve deeper, consider incorporating specific case studies of manufacturers, detailed descriptions of manufacturing processes, and in-depth analysis of specific glove box applications. Additionally, exploring the challenges and future trends in the industry can add value to the article.
Would you like to focus on a specific aspect of anaerobic glove box manufacturing or explore a particular application in more detail?