The glove box, a seemingly simple enclosure, is a testament to human ingenuity in creating controlled environments. When precision, purity, and isolation are paramount, the stainless steel glove box emerges as the preferred choice. This article delves into the intricacies of manufacturing these critical enclosures, focusing on a German factory renowned for its adherence to exacting engineering principles.
The glove box is more than just a chamber; it is a mechanical system designed to interface with the human operator while maintaining a controlled atmosphere. This delicate balance requires a profound understanding of materials science, fluid dynamics, and human factors engineering.
Materials: The Foundation of Integrity
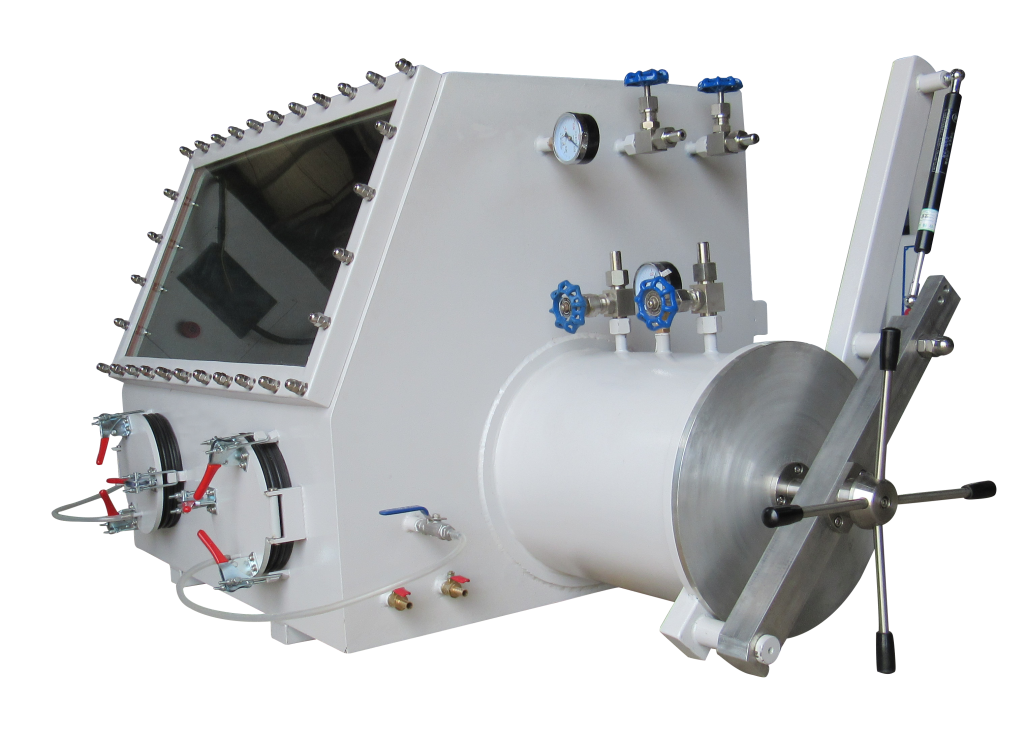
Stainless steel, the backbone of the glove box, is a material meticulously chosen for its corrosion resistance, strength, and biocompatibility. The alloy composition, specifically designed for this application, offers a unique blend of properties. Austenitic stainless steel, with its face-centered cubic crystal structure, provides excellent formability and weldability, crucial for the complex geometries of a glove box.
The selection of stainless steel grade is a critical decision. For instance, 316L, with its enhanced resistance to chloride-induced corrosion, is often favored for pharmaceutical applications. The material’s microstructure, characterized by grain size and precipitate distribution, significantly influences its mechanical properties and corrosion behavior.
Beyond the primary material, a glove box is a composite of various components. Seals, typically made of elastomeric materials like Viton or EPDM, must exhibit excellent chemical resistance and compression set resistance. Gaskets, often fabricated from silicone or PTFE, provide additional sealing integrity. The choice of these materials is dictated by the specific operating environment and the nature of the materials handled within the box.
Design Considerations: A Symphony of Engineering
The design of a stainless steel glove box is a complex interplay of form and function. The chamber’s geometry is crucial in minimizing dead spaces where contaminants can accumulate. Sharp corners and crevices are meticulously avoided to facilitate cleaning and prevent particle retention.
The glove ports, the operator’s interface with the controlled environment, demand careful consideration. Their size, shape, and location influence both operator comfort and contamination risk. Ergonomic design principles are applied to minimize operator fatigue and maximize productivity.
Pressure management is a critical aspect of glove box design. Whether operating under positive or negative pressure, the system must maintain a stable differential to prevent ingress or egress of contaminants. This requires precise control of airflow and filtration.
The glove box’s internal environment is often subjected to rigorous conditions, including temperature and humidity extremes. The design must ensure structural integrity and material compatibility under these demanding circumstances. Finite element analysis (FEA) is employed to predict stress distributions and identify potential weak points.
Manufacturing Precision: A Craftsman’s Approach
The production of a stainless steel glove box is a multi-step process that demands meticulous attention to detail. The manufacturing facility is typically classified as a cleanroom to minimize particulate contamination.
Sheet metal fabrication is the foundation of the glove box structure. Laser cutting ensures precise dimensions and eliminates burrs. The cut components are then formed into complex shapes using bending and forming machines. Welding, often TIG or laser welding, joins the components with precision and strength.
The glove ports are integrated into the chamber wall, requiring specialized tooling and welding techniques. The seamless integration of the glove and the port is critical for maintaining the integrity of the seal.
Polishing and passivation are essential steps in achieving the desired surface finish. These processes remove surface contaminants and create a protective oxide layer, enhancing corrosion resistance.
Quality Assurance: A Commitment to Excellence
A robust quality assurance program is indispensable in glove box manufacturing. Materials are subjected to rigorous incoming inspection to verify their conformity to specifications. Dimensional checks, surface finish evaluation, and material testing are conducted at various stages of production.
Leak testing is a critical quality control parameter. Helium leak detection is commonly employed to identify even the smallest leaks. Pressure decay testing is used to assess the overall sealing performance of the glove box.
The finished product undergoes a final inspection, including functionality testing and documentation. The manufacturer often provides comprehensive documentation, including design drawings, material certificates, and test reports.
Applications: A Versatile Tool
Stainless steel glove boxes find applications across a wide spectrum of industries. In research laboratories, they provide controlled environments for handling sensitive materials. In the pharmaceutical industry, they ensure product purity and operator safety. In electronics manufacturing, they protect components from contamination.
The specific configuration of a glove box is tailored to the application. For example, a glove box used in a pharmaceutical cleanroom may incorporate additional features such as laminar airflow and HEPA filtration.
Future Trends: Innovation and Sustainability
The glove box industry is continually evolving. Advancements in materials science are leading to the development of new alloys with enhanced properties. For instance, high-strength, low-alloy stainless steels offer the potential for lighter and more cost-effective glove box designs.
Automation and robotics are being increasingly adopted in the manufacturing process to improve efficiency and consistency. Digital technologies, such as augmented reality and virtual reality, are being explored to enhance operator training and maintenance.
Sustainability is a growing concern. Efforts are being made to reduce the environmental impact of glove box manufacturing through recycling and energy-efficient processes. The development of biodegradable glove box materials is an emerging area of research.
The stainless steel glove box is a sophisticated piece of equipment that represents a harmonious blend of materials science, mechanical engineering, and manufacturing expertise. Its role in safeguarding products and processes is indispensable in modern industry. As technology continues to advance, we can expect even more innovative and efficient glove box designs to emerge.
Note: To further enhance this article, consider incorporating specific examples of glove box applications, detailed descriptions of manufacturing processes (with diagrams or images), and case studies of successful glove box implementations. Additionally, exploring the regulatory framework governing glove box design and manufacturing can add depth to the article.
Would you like to focus on a specific aspect of glove box manufacturing or explore a particular application in more detail?